Rubberized Asphalt
A chemically Engineered Crumb Rubber product called Elastiko ECR is fed into your plant during mix production, just like a fine aggregate. The heated binder reacts with the ECR during mixing, storage and transport. The delivered mix lays and performs like a polymer-modified pavement, but at a fraction of the cost.
ECR reduces the cost of a two grade bump: by $2-$4 per mix ton. It makes your plant run faster compared to polymer modified mixes: lower mix viscosities permit 10-15% faster plant throughput. Also, it generates less waste: mixes leave the truck with almost no residue in the bed, reducing truck cleanout waste.
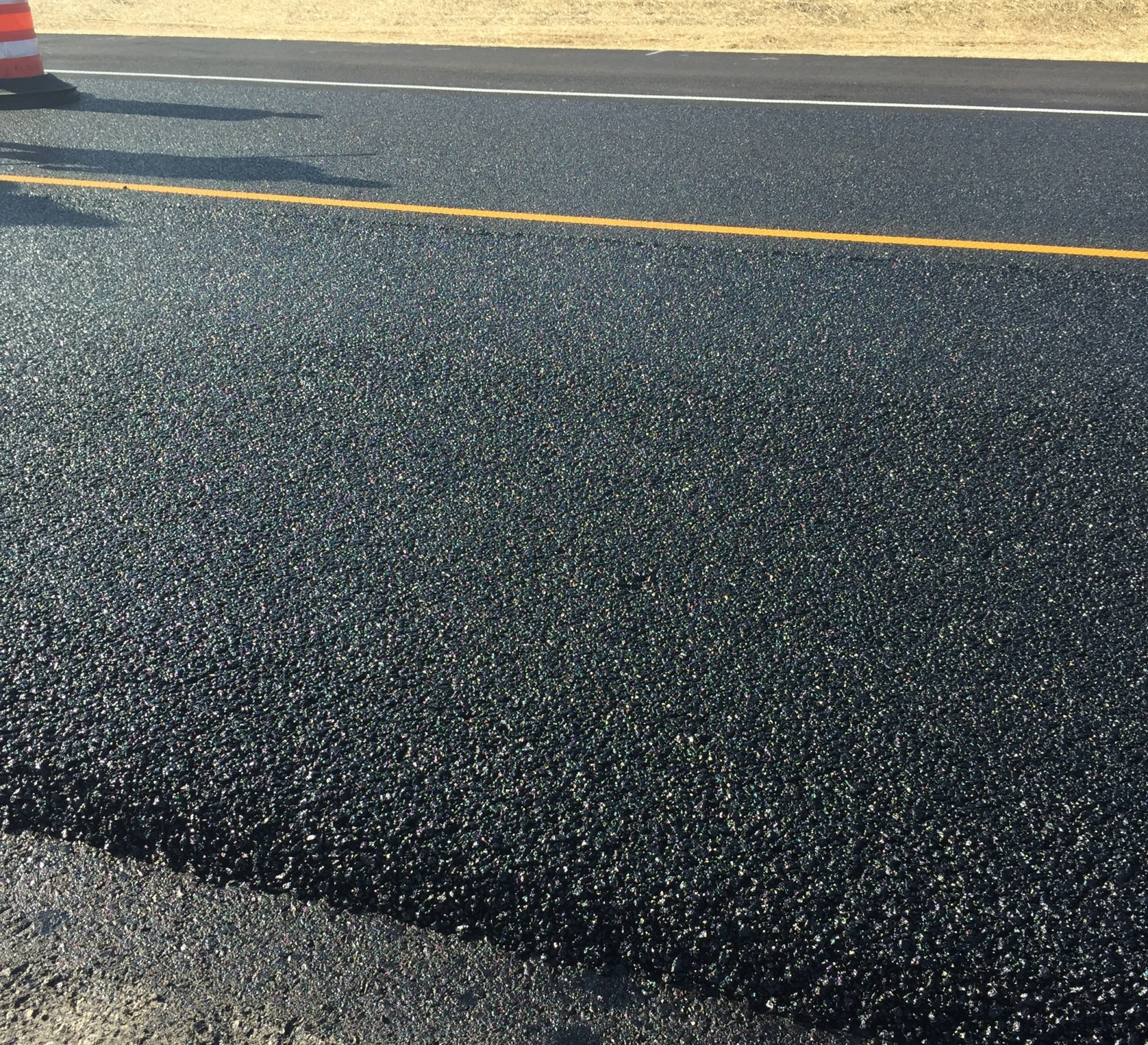
Rubberized Asphalt: How It’s Made
Elastiko is applied to the crumb rubber in order to improve the handling and workability characteristics of the mix. Also rubberized asphalt consumes an estimated 220,000,000 pounds of tires annually. More states are starting to see the benefits of rubber in asphalt.
In a comparison with a polymer modified mix design, the Elastiko Rubber Asphalt-modified mix exhibited similar rutting and cracking resistance. With the standard hot mix design, the ECR-modified mix out-performed the standard mix in both rutting and cracking resistance.
Wolf Lake Terminal, Hammond, IN
The access road to a major rail to truck transfer facility was repaved with Dry Mix and Hot Mix Asphalts in adjoining sections. After seven years of service, Dry Mix asphalt pavements are in good to excellent condition, showing no material thermal cracking damage. Hot mix pavement failed and requires replacement.
Rubberized Asphalt Benefits
• ECR reduces the cost of a twograde bump: by $2-$4 per mix ton
• ECR makes your plant run faster compared to polymer modified mixes: lower mix viscosities permit 10-15% faster plant throughput
• ECR generates less waste for interstate highway projects: mixes leave the truck with almost no residue in the bed, reducing truck cleanout waste
• ECR can extend your paving season: ECR mixes can allow paving and compaction in colder temperatures
• ECR allows more efficient compaction: ECR mixes typically require 10-20% fewer roller passes to achieve compliant compaction
• ECR pavements work well in thinlay applications: Compared to standard unmodified hot mix asphalt, ECR pavements can achieve greater durability with thinner lifts.
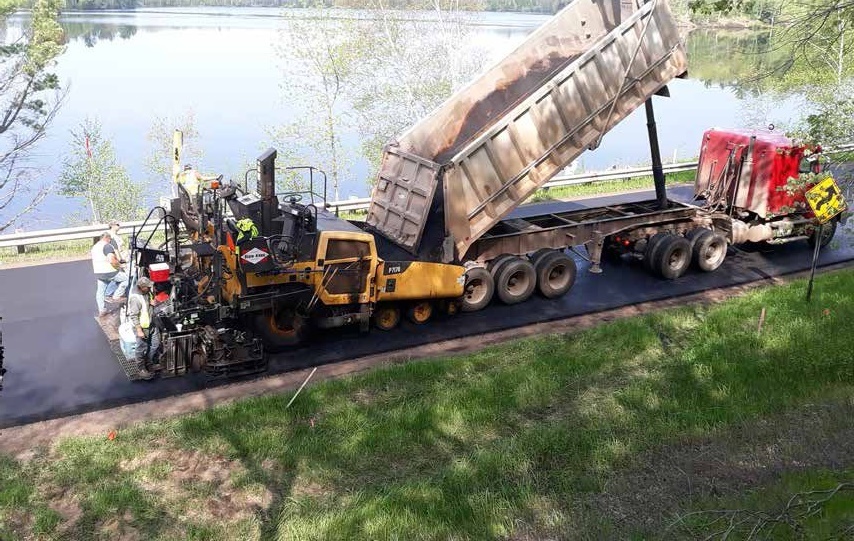
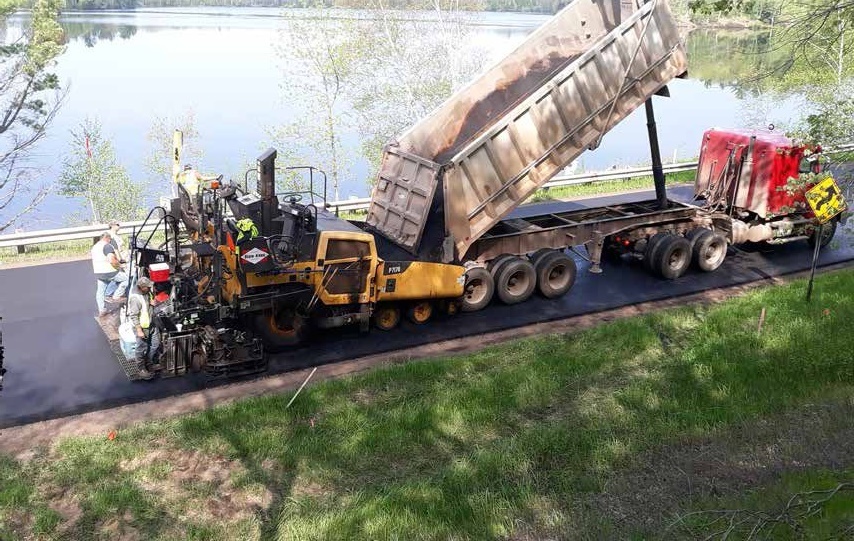
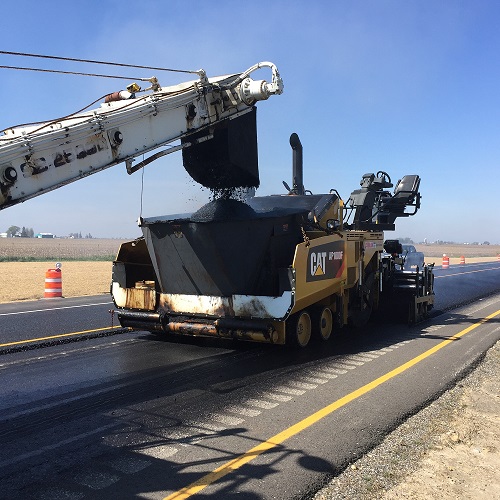
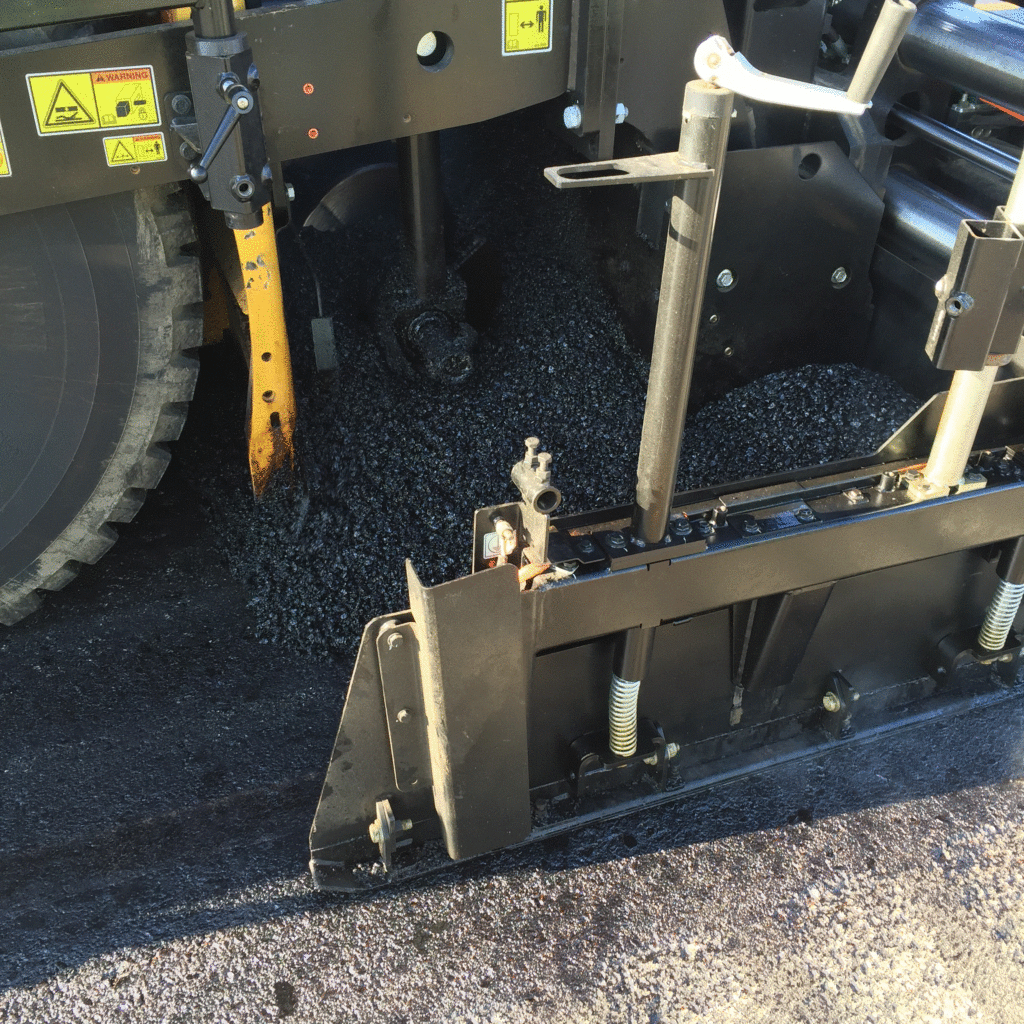