I-39 in Beloit, WI Dry Process Rubber Asphalt
In late 2017, WIDOT approved the use of a WIDOT WI-12.5 N75 SMA mix modified with ElastikoTM ECR as an alternative for a polymer modified mix. The project provided the opportunity for WIDOT and the contractor to evaluate the production characteristics of the mix, the accuracy of the feeder and placement characteristics of the mix at low temperatures. This project was a follow-on to the WIDOT dry process rubber asphalt placement on I-88 in Illinois in conjunction with the Tollway.
The standard production mix for this project used a 70 -28 polymer modified binder with low levels of RAP in the mix design. The ECR-modified mix included the same amounts of RAP and an 11% by weight of 58 -28 virgin binder in the job mix formula, which included a 4.2% virgin binder content and 9 lbs. of rubber per mix ton. Lab testing indicated comparable rutting and cracking performance with both mix designs.
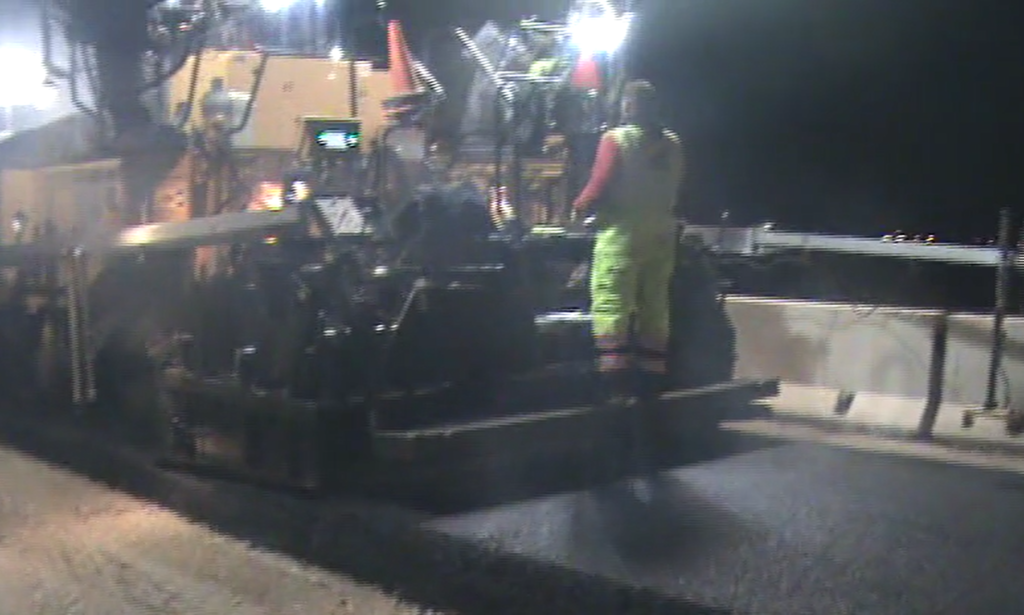
Mix production and paving took place on November 28 between 7 and 11 PM, with temperatures between 43 F at the start of paving and falling to 39 F at the completion of paving. The plant ran at 340 F for the project because paving was occurring on a cold day, and trucking time from plant loading to the paver ran about 45 minutes. The loads were hauled in covered, uninsulated dump trucks. The mix temperatures coming out of the paver averaged approximately 250 F.
Plant management reported no issues with production. The ECR feeder was within 0.2% of the required amounts to meet JMF design and quantity requirements. The feeder tracked and recorded inputs every 45 seconds during the production run, and the overall feeder accuracy is in line with results from other projects in various parts of the US. The cold weather did not impact the feeder accuracy, ECR flow characteristics and mix handling characteristics.
Field compaction of the mix at cold temperatures caused no issues. The roller operator reported lower pass count compaction in compliance with contract density requirements.
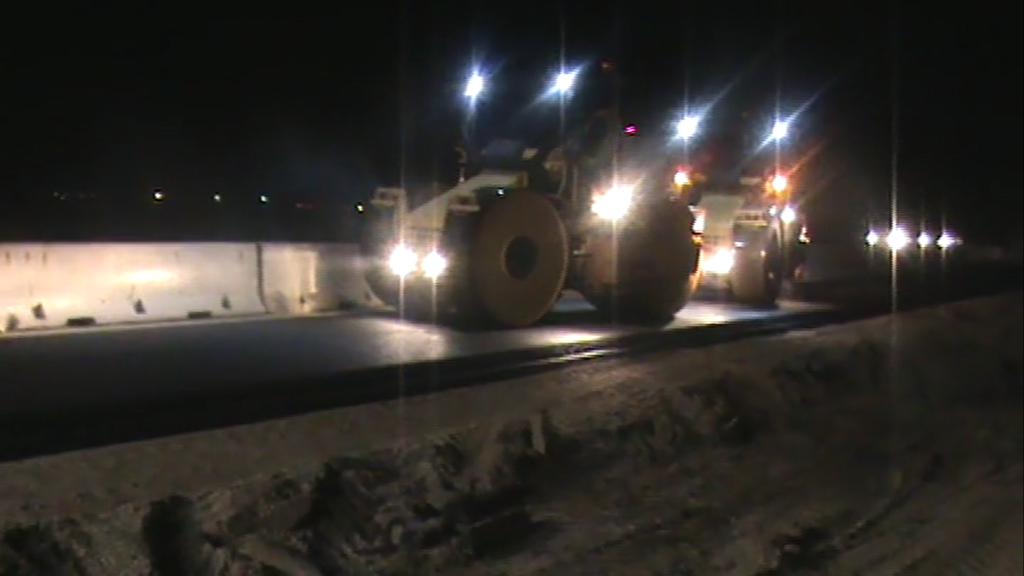
The produced and placed ECR pavement had no field performance issues when placed in service. Like a host of similar projects placed all over the US, ECR and polymer pavements performed comparably. The ECR significantly reduced the cost of modified asphalt mix designs while maintaining performance levels comparable with polymer modified asphalts.