Crumb Rubber Pavement Introduction
Production of a crumb rubber pavement comprises a series of activities, such as materials production, construction, maintenance etc., all of which have environmental impacts. Life Cycle Assessment (LCA) can track and quantify the environmental impacts of both individual and total activities of products. It helps identify the activities with the highest environmental burdens within the life cycle of the product, or point to 2 hotspots and clarify the most environmentally effective strategies among various options. Such advantages make LCA a methodology frequently used to assess the environmental impacts of asphalt pavements. The increasing number of vehicles leads to increasing amounts of tires disposed.
Current solutions to disposing waste tires include the energy recovery (use tires as alternative fuels in cement kilns), chemical recovery (pyrolysis/thermolysis) and granulate recovery (shredding) [1]. Rubberized asphalt pavement is an increasingly popular method that uses the crumb rubber (CR) from waste tires. CR can be either added by wet process or dry process into asphalt mixtures. Although CR asphalt pavements have received positive feedback in other countries [2], their potential ecological benefits/losses for Switzerland are still not clarified. Therefore, in this paper we use LCA to assess the environmental performance of CR modified asphalt pavements in Switzerland. LCA allows to investigate the environmental strengths and weaknesses of using CR. Evaluations are performed through the case study of Swiss semi dense asphalt (SDA) pavements.
Asphalt mixtures
Three types of asphalt mixtures for the wearing courses are prepared in plant. The mix designs are based on Swiss standard SNR 640436 for SDA 4-12 (maximum particle size: 4 mm, air voids content: 10-14%) [3], and their details are shown in Table 1.

Mechanical performance of asphalt mixtures
To compare the mechanical performance of investigated asphalt mixtures, the cooperated study conducted the water sensitivity test (EN 12697-12) and wheel tracking test (EN 12697-22) [4]. The results showed that the indirect tensile strength ratios of all the specimens are comparable, ranging from 76 to 81%; the rutting ratio of Ref. and CR1.0 are both 6.0% at 30 000 cycles, while CR0.7 has less rutting ratio of 4.4% [4]. Based on the available test results, this initial study assumes that the CR wearing courses have the same service life as that of the reference. In the future study, further tests need to be employed to estimate more accurate service life.
Life Cycle Assessment of Crumb Rubber Pavement
The international standard ISO 14040 divides LCA into four steps: goal and scope definition, inventory analysis, impact assessment and interpretation [5]. For the case of wearing courses, all the four steps are explained as follows:
Goal and Scope Definition of Crumb Rubber Pavement
LCA is used to quantify and compare the environmental impacts of reference and CR wearing courses. The functional unit (FU) is constituted by the wearing course with the dimensions of 1 km length, 7m width and 30 cm depth. The effects of dimension, service life, traffic volume, weather and other pavement layers are assumed to be identical for all the wearing courses studied. Fig. 1 shows the system boundary, including the processes of crumb rubber pavement and rubber/coal incineration. It shall be noted that the maintenance is equal to end-of-life for wearing courses because both two processes demolish the used wearing courses and transport them to the recycling plant. Due to lack of reliable data of emissions, the use phase is not considered in the analysis.
The crumb rubber pavement is originally incinerated in Swiss cement kilns where it replaces coal. To make a fair comparison of the current reference situation and scenarios of CR use in pavements, system expansion was used as an allocation approach. The following three scenarios are discussed for comparison:
(1) CR wearing course with 3.0 t of rubber from waste tires + incinerating 1.4 t of rubber and 3.3 t of coal (to substitute for the diverted tires in the kiln); (2) CR wearing course with 4.4 t of rubber + incinerating 4.8 t of coal; (3) Reference wearing course + co-processing of 4.4 t of rubber in cement kilns.
Within the functional unit, 3.0 and 4.4 t of rubber account for 0.7 and 1.0% of asphalt mixtures by weight, respectively; the energies generated by 3.3 and 4.8 t of coal are equal to that produced by 3.0 and 4.8 t of rubber, respectively. The calorific values of coal and rubber are assumed to be 31.4 and 28.7 MJ/kg, respectively, and the carbon content of coal is 81% [6-7].
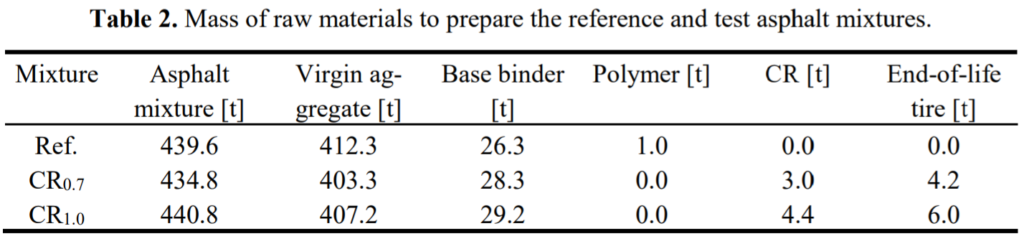
Materials production: based on the functional unit, Table 2 presents the quantity of raw materials to prepare each type of asphalt mixtures. The input/output data of base binder and polymer are obtained from the report of Eurobitume [9]. According to the industrial partner, the grinding of 1 t of waste tires produces 0.73 t of CR (rest parts of tires are steel wires and fibers) and consumes 308 kWh of electricity. The data of aggregates and electricity are determined by the ecoinvent database.
Asphalt mixing: as mentioned in previous case study in Switzerland [8], the incorporation of crumb rubber pavement by dry process does not increase the energy consumption of mixing; the production of 1 t of asphalt mixtures consumes 8.6 kWh of electricity and 216.3 MJ of natural gas (assuming the calorific values of natural gas is 49.4 MJ/kg [9]). The environmental impacts of natural gas are provided by the ecoinvent database; qualitative measurements from the industrial partner shows that CR plays very limited role in increasing the total emissions during mixing. Therefore, such emissions are assumed to be same for all the asphalt mixtures.
Construction: the construction of wearing course requires 1.48, 1.50, and 1.49 × 104MJ per FU for scenario (1)-(3), respectively [8]. These amounts of energy are consumed by pavers, materials’ transfer vehicles, rollers and electricity generators, and provided by diesels (impacts of diesels are determined by ecoinvent). Due to lack of data, the emissions of asphalt mixtures during the construction are not included. Maintenance: the use of milling machine and electricity generators consume 11.54 MJ and 4.75 MJ (from diesel) tonne of wearing courses [8]. The overlaying of new wearing course is not included because it is identical in all scenarios and therefore not relevant for the comparison.
Transportation: the distances among all the relevant places (rubber manufacturer, mixing plant, construction site etc.) are based on their actual geographical locations in Switzerland or abroad, and they add up to 7.02, 7.15, and 6.92 × 104 tkm per FU for scenario (1)-(3). A 25 t lorry is assumed to be the only method of transport, of which the impacts are provided by the ecoinvent database.
Rubber/coal incineration: the emissions of coal incineration are derived from the elemental composition of hard coal from Oberschelp et al. [6]; the impacts of rubber incineration are based on the ecoinvent.
Impact Assessment
The impacts investigated in this article include the cumulative energy demand (CED) and global warming potential (IPCC GWP 100a). The collected data are integrated by Simapro 9.0.0.48 to quantify the target environmental impacts.
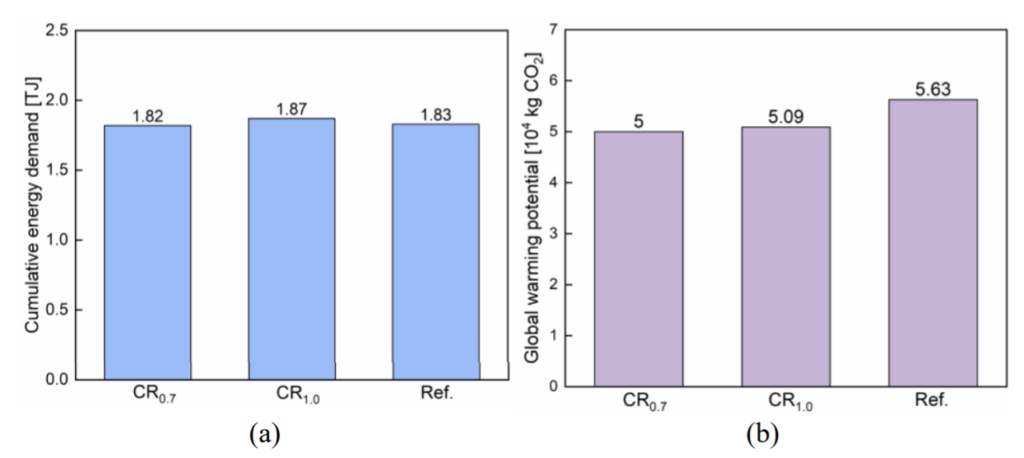
Quantitative results of CED and GWP for all the scenarios are shown in Fig. 2. It can be seen that the CED values between the reference and crumb rubber pavement wearing courses are quite comparable, implying that the use of CR in both wearing courses and cement kilns have few differences in energy consumption. However, the emissions of greenhouse gases (GHG) from CR wearing courses are lower than that of the reference.
Table 3 compares the GHG emissions of all scenarios in different phases. The largest gap of GHG emissions between reference and CR wearing courses is in the binder preparation. The reason is that the reference wearing courses use polymer modified binder, in which the production of polymer release huge amount of GHG. While the CR wearing courses use base binder, which eliminates the GHG cause by polymer production.
Conclusion
This study employs LCA to compare the environmental impacts of reference and CR wearing courses in Swiss SDA pavements. Asphalt mixtures are prepared in plant and mechanical tests are conducted to investigate the mechanical performance of reference and CR mixtures. CR comes from waste tires that are originally incinerated in cement kilns. The analyzed scenarios include both the rubber/coal incineration and the life cycle of wearing courses. The results showed that the cumulative energy demands are comparable between the reference and CR wearing courses, while the climate change impacts of CR wearing courses are lower than that of the reference. The main reason is the greenhouse gas emissions caused by polymer production in the life cycle of reference wearing courses. From the environmental point of view, the results present a high potentials of CR as an alternative performance enhancing material of wearing courses and alternative method to dispose of waste tires in Switzerland.