Rubber Asphalt Successfully Laid in Switzerland
With millions of tons of Dry Process Rubberized Asphalt successfully laid and counting in the US, Asphalt Plus is turning its sights internationally. Tyre Recycling Solutions (TRS) in partner with Empa’s Concrete and Asphalt lab have recently started to explore what benefits Rubberized Asphalt could have in Switzerland. With all the success Asphalt Plus has been having in the US with the dry process technology, the recognition is spreading fast.
With rapidly rising numbers of projects using Dry Process Rubberized Asphalt, we are seeing lots of comparisons side by side to Polymer roads. The overwhelming results of the Rubber Asphalt outperforming Polymers is showing us a new opportunity for better, longer lasting roads using rubber. Along side with rubber improving the quality of asphalt roads, we are also seeing a huge benefits to the environment. Being the largest market for ground tiers, rubberized asphalt consumes an estimated 220,000,000 pounds or around 12 million tires annually.
The testing done in the project with TRS and Empa’s Concrete and Asphalt lab is another chance to show just how reliable and sustainable dry process rubberized asphalt is paving a path to the future. Read more about this testing in the article below.
Asphalt Plus LLC is a specialty chemical and equipment manufacturing company headquartered near Chicago, IL. We produce Elastiko engineered crumb rubber additive for rubberized asphalt application. Over the past two decades, extensive lab also field work has created a new binder modification option for asphalt producers. Dry process rubber modification of asphalt also allows you to produce rubber-modified mixes that perform like polymer-modified mixes without the use of terminal blending. Asphalt Plus engineered rubber has endured a wide range of harsh climate & road use conditions.
As a result of these situations, Asphalt Plus has performed impeccably well with nearly 6 million tons of placed Dry Mix Asphalt. We have assisted the auto manufacturing industry, the Department of Defense, Energy and Interior in cost-effectively reducing both their operating costs and their environmental footprint in a wide range of activities.
• ECR reduces the cost of a twograde bump: by $2-$4 per mix ton
• ECR makes your plant run faster compared to polymer modified mixes: lower mix viscosities permit 10-15% faster plant throughput
• ECR generates less waste: mixes leave the truck with almost no residue in the bed, reducing truck cleanout waste
• ECR can extend your paving season: ECR mixes can allow paving and compaction in colder temperatures
• ECR allows more efficient compaction: ECR mixes typically require 10-20% fewer roller passes to achieve compliant compaction
• ECR pavements work well in thinlay applications: Compared to standard unmodified hot mix asphalt, ECR pavements can achieve greater durability with thinner lifts.
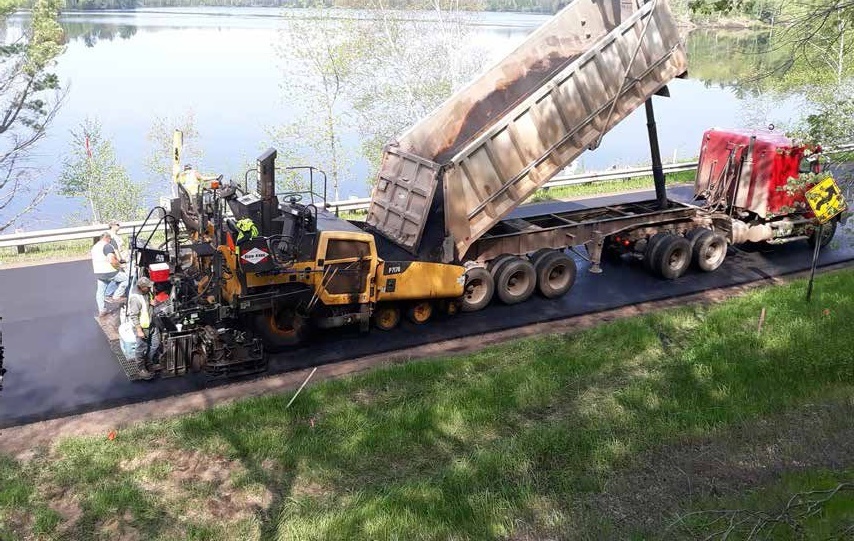
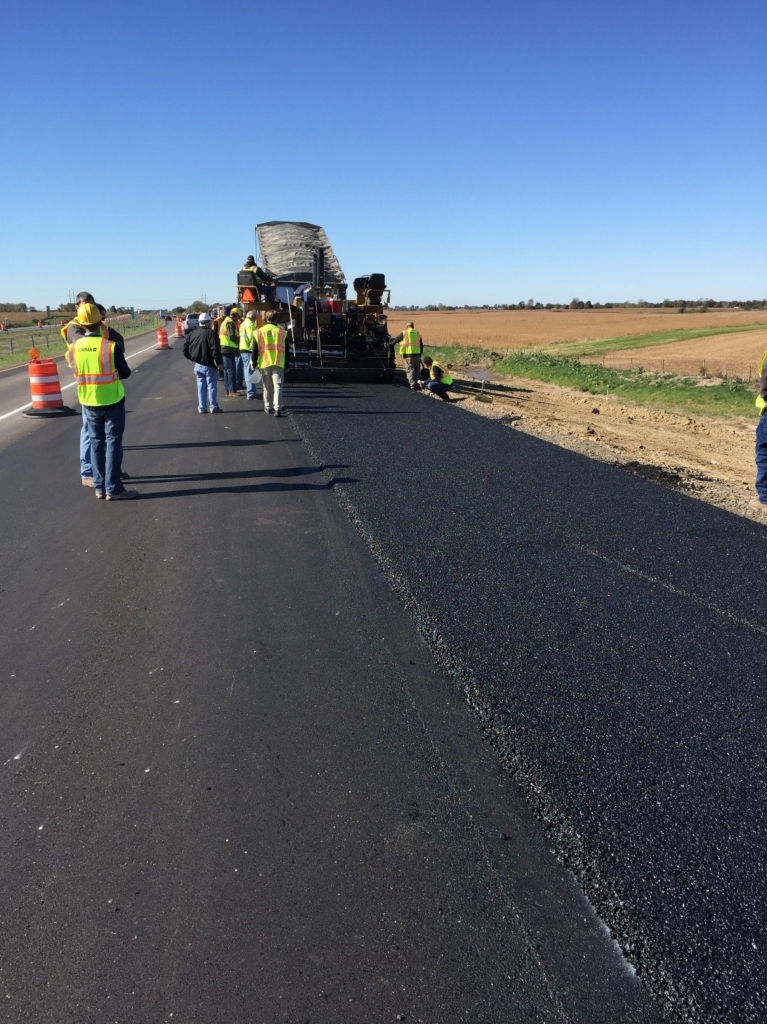
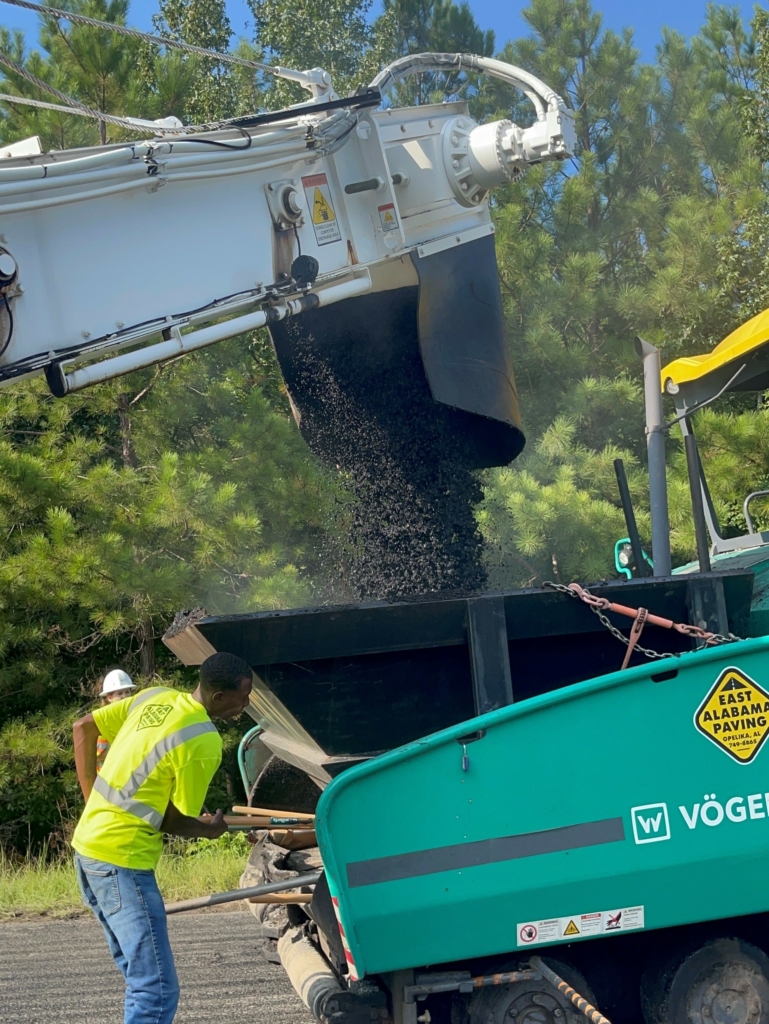
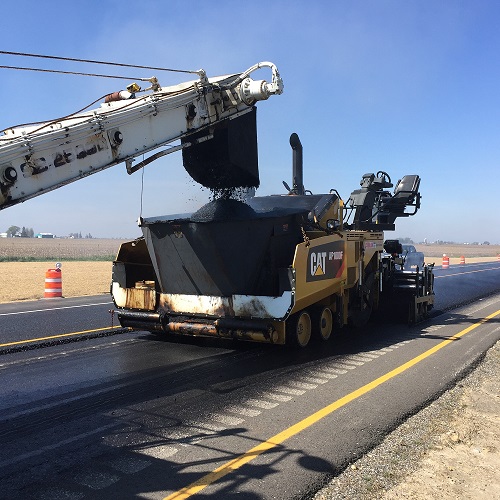
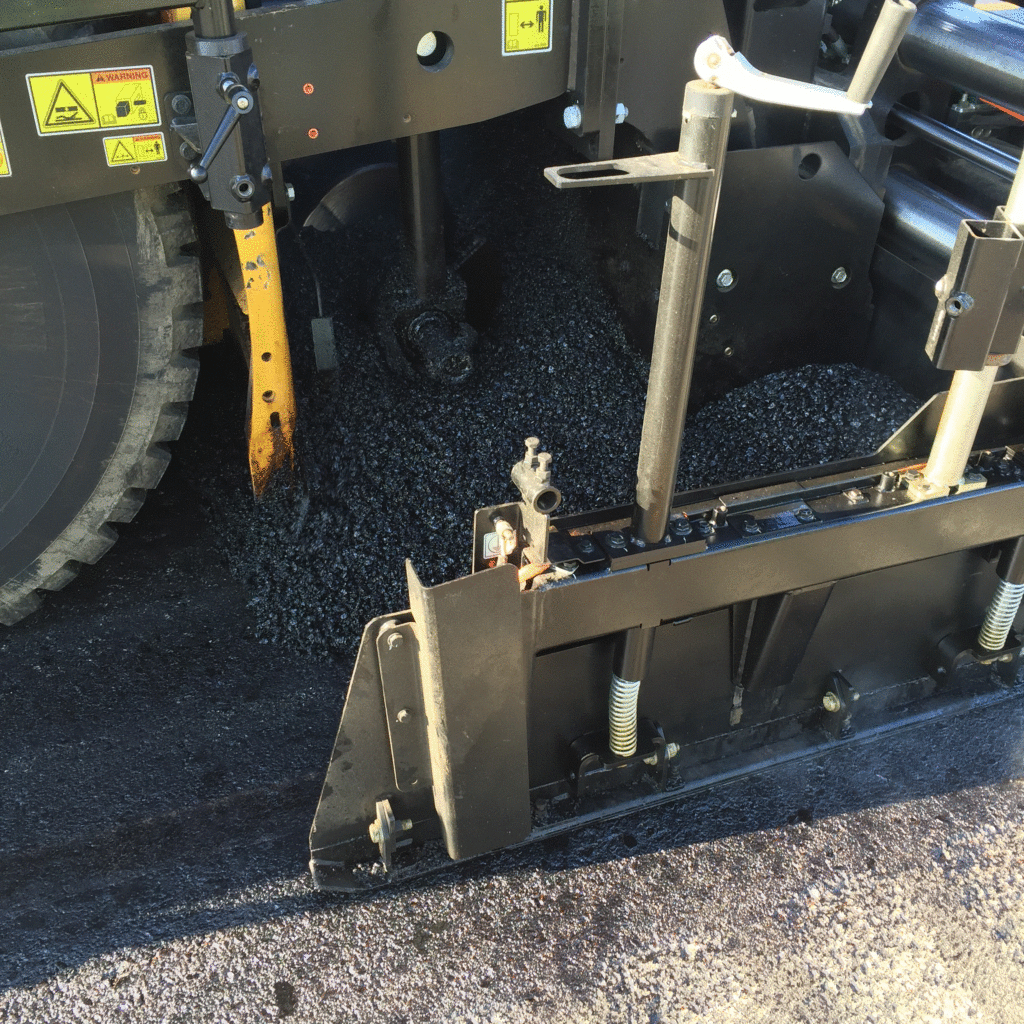